DXへの関心が高まる製造業界でも、本来のDXに取り組めている企業は多くありません。製造業のDX実現には何が必要か、合同会社アルファコンパス 代表CEOの福本勲さんをお招きし、当社の製造部門担当と対談しました。全3編におよぶ本シリーズのうち、Part2では、デジタル化の目的についてお話ししていきます。
目次
前回のパートはこちら
対談者紹介
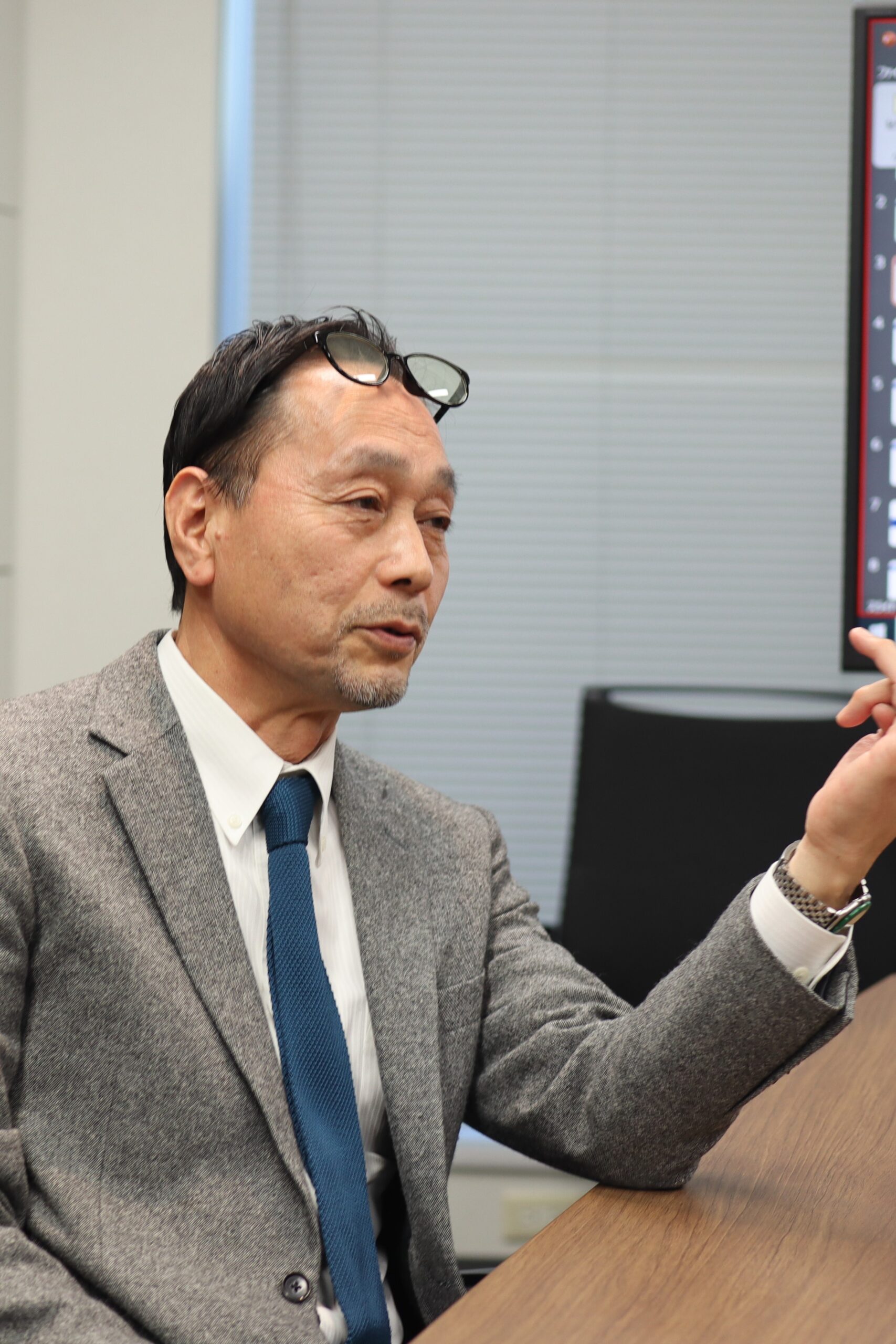
NSW株式会社
荒井 毅一
大手製造メーカーに勤務後、TPS(トヨタ生産方式)の社内展開、新規事業立上げなどを経てNSWに入社。国内・海外工場システム構築・展開など、特に製造分野に深い知見を持ち、顧客目線での、お客様のDX推進を支援しています。
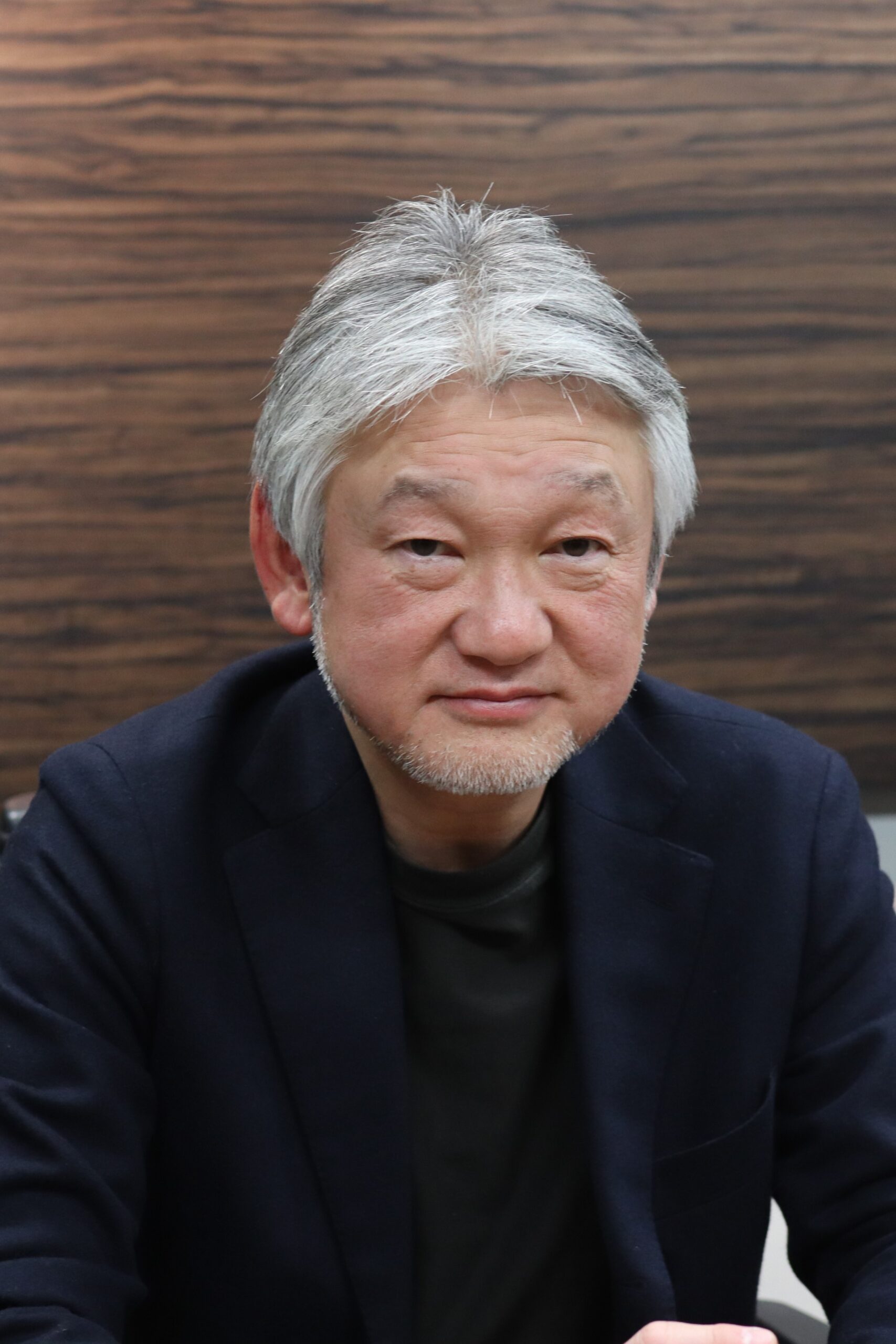
合同会社アルファコンパス
福本 勲
合同会社アルファコンパスの代表CEOを務め、製造業のデジタルトランスフォーメーションやマーケティング支援に注力しています。また、中小企業診断士としても活動し、講演や執筆を通じて製造業の変革を推進しています。
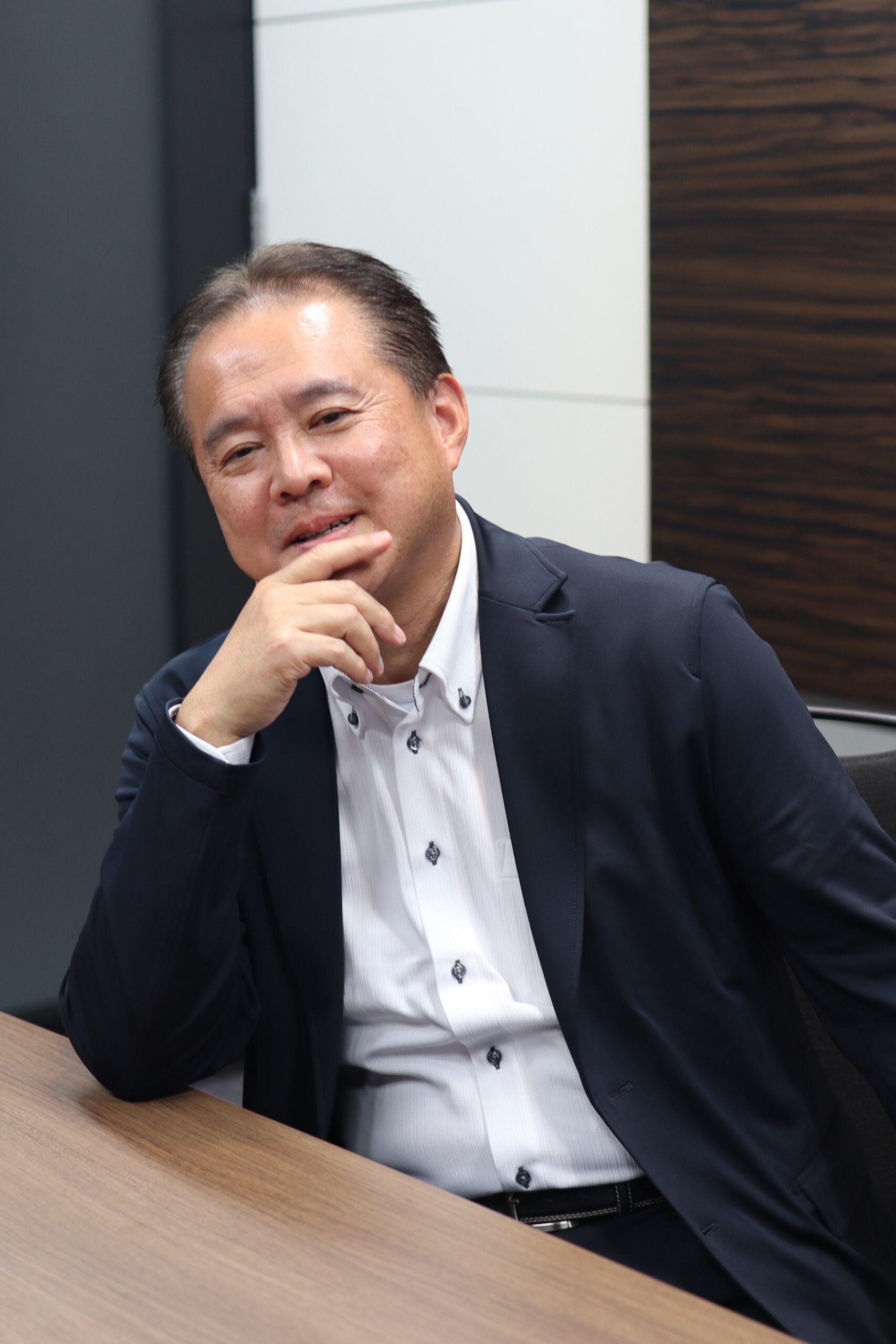
NSW株式会社
堀内 忠彦
大手精密機械メーカーに勤務後、コンサルタントを経てNSWに入社。お客様と共創、伴走するコンサル業務で製造業主体のDXを推進。技術士(経営工学部門)として、生産業務プロセス改善、SCM、現場改善指導等にも従事しています。
デジタル化しても、人の作業はなくさない
*XVL(eXtensible Virtual world description Language)
XVL (eXtensible Virtual world description Language) は、ラティス・テクノロジー株式会社が開発した超軽量3Dデータフォーマット。3D CADデータを数百分の1にまで軽量化し、形状データと製品構成、寸法、注記などの情報を一つのファイルにまとめることができます。
付加価値の先に、賃金の上昇がある
*引用:厚生労働省「令和4年版 労働経済の分析 -労働者の主体的なキャリア形成への支援を通じた労働移動の促進に向けた課題-(全体版)」, p.99
物価の伸びを考慮した実質賃金をみると、1991年の賃金を100とすると、2020年の日本は103.1となっており、イタリアを除く各国と比較すると賃金の伸びが低くなっていることが分かる。さらに、リーマンショック後の2010年以降の実質賃金は、イギリスやイタリアなど日本以外でも実質賃金が伸び悩む国もあることが分かる。
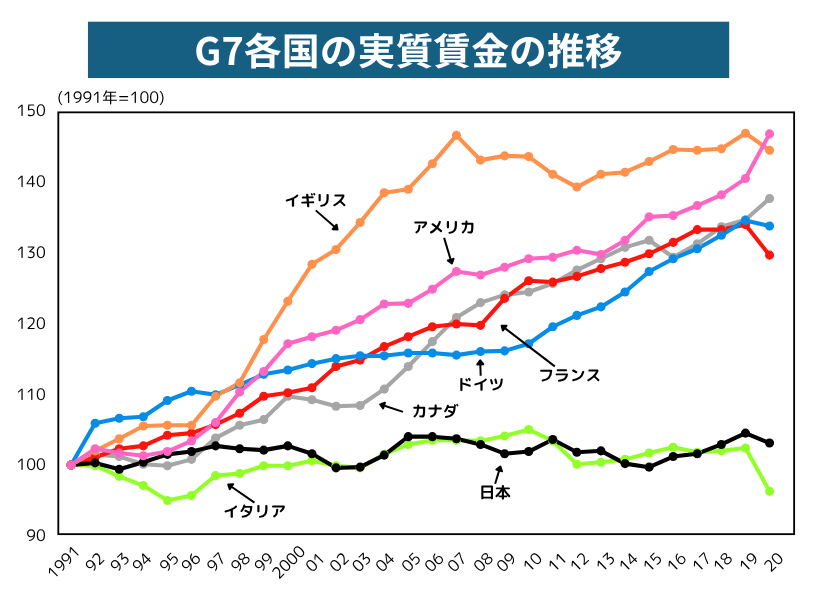
資料出所 OECD.StatにおけるAverage Annual Wagesにより作成。購買力平価ベース。
(注)
1)1991年を100とし、推移を記載している。なお、OECDによるデータの加工方法が不明確なため、厳密な比較はできないことに留意。なお、我が国の計数は国民経済計算の雇用者所得をフルタイムベースの雇用者数、民間最終消費支出デフレーター及び購買力平価で除したものと推察される。
2)名目賃金は、OECDが公表する実質賃金に消費者物価指数の総合指数を乗じることで算出している。
(注)
1)1991年を100とし、推移を記載している。なお、OECDによるデータの加工方法が不明確なため、厳密な比較はできないことに留意。なお、我が国の計数は国民経済計算の雇用者所得をフルタイムベースの雇用者数、民間最終消費支出デフレーター及び購買力平価で除したものと推察される。
2)名目賃金は、OECDが公表する実質賃金に消費者物価指数の総合指数を乗じることで算出している。
引用:厚生労働省「令和4年版 労働経済の分析 -労働者の主体的なキャリア形成への支援を通じた労働移動の促進に向けた課題-(全体版)」, p.99
*OECD 年間平均賃金(UCD)
OECD(経済協力開発機構)が集計している、加盟国(38ヵ国)別の2024年の年間平均賃金(UCD)。OECD加盟国全体の平均と比較しても、日本の年間平均賃金は低くなっている。
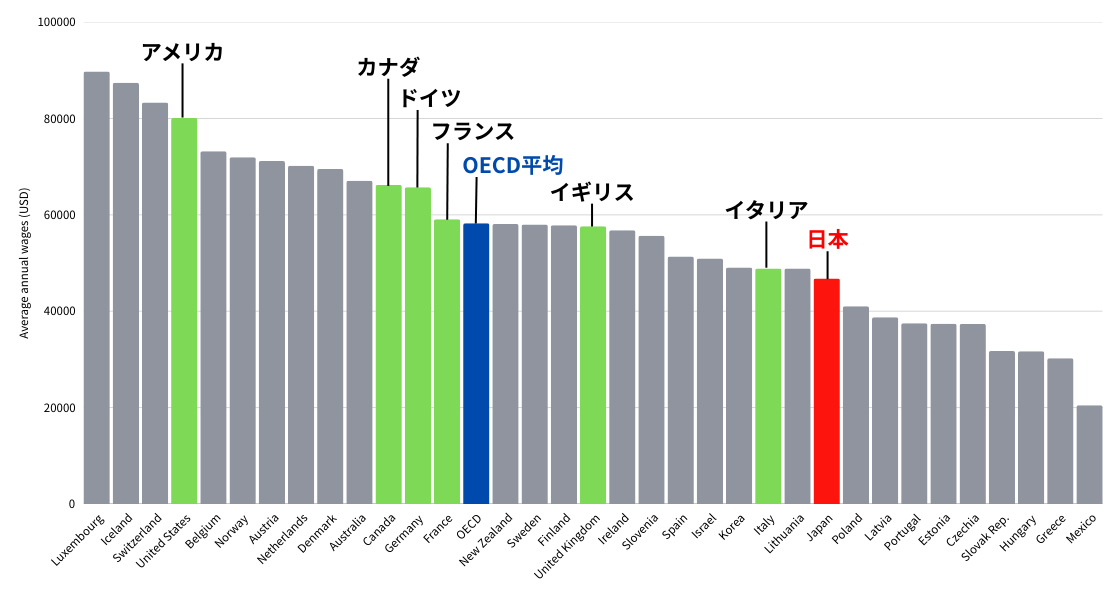
日本に合ったERPの導入
*引用:ジャパンSAPユーザーグループ「日本企業のためのERP導入の羅針盤~ニッポンのERPを再定義する~」, 2019, p2

これまでの20数年間、日本企業は、レガシーシステムの刷新とBPR推進を目指し、こぞって基幹業務統合型アプリケーション(ERP)のパッケージであるSAP R/3の導入を行ってきた。今や、SAP ERPの導入企業は、日本で2,000社を超えると言われている。
しかしながら、導入したSAPを充分に活かして、本来の目的であったリアルタイム経営、データを活用した経営を実現している企業は必ずしも多くはないのではないか。SAPを導入したものの、業務プロセスを変革することが出来ず、結局アドオンを多数開発し、標準化にはほど遠く、データ活用もままならず、維持管理に多大なコストをかけているという声をJSUG会員企業からも多く聞いている。
しかしながら、導入したSAPを充分に活かして、本来の目的であったリアルタイム経営、データを活用した経営を実現している企業は必ずしも多くはないのではないか。SAPを導入したものの、業務プロセスを変革することが出来ず、結局アドオンを多数開発し、標準化にはほど遠く、データ活用もままならず、維持管理に多大なコストをかけているという声をJSUG会員企業からも多く聞いている。
引用:ジャパンSAPユーザーグループ「日本企業のためのERP導入の羅針盤~ニッポンのERPを再定義する~」, 2019, p2
*日本企業のERP導入の課題・問題点
(1)ERPの稼働自体が目的になっている
(2)プロジェクトの理念、目的が明確になっていない
(3)膨大なアドオンが作られている
(4)アドオンが増えたために、コストがかかりすぎている
(5)製品に対する知識や人的リソースが足りない
(6)IT部門のあり方や、パートナーとの関係自体に問題がある
(7)導入企業の中に権限を持つビジネスプロセスオーナーがいない
引用:ジャパンSAPユーザーグループ「日本企業のためのERP導入の羅針盤~ニッポンのERPを再定義する~」, 2019, p13
*Plex製造実行システム(MES)
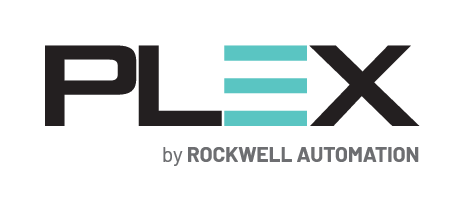
Rockwell Automation社の提供するクラウド型の製造実行システム(MES)。製造現場から経営管理まで、あらゆる情報を可視化・自動化して、スマートマニュファクチャリングを実現します。
経営層と現場を繋げる人
他のパートはこちらから
NSWが実現するDX
NSWは長年にわたる幅広い業種での豊富な実績と経験を生かし、お客様の潜在課題を多彩なデジタル技術で柔軟に解決することで、よりよい未来を築いていきたいと考えています。NSWの提供するスマートファクトリーソリューションもぜひご覧ください。