DXへの関心が高まる製造業界でも、本来のDXに取り組めている企業は多くありません。製造業のDX実現には何が必要か、合同会社アルファコンパス 代表CEOの福本勲さんをお招きし、当社の製造部門担当と対談しました。全3編におよぶ本シリーズのうち、Part1では、そもそも全体最適とは何なのかについてお話ししていきます。
目次
はじめに ~製造業の現状と課題~
2024年版ものづくり白書*では、製造業におけるDXについて「全体最適までいかず、個別工程のカイゼンに留まっている企業が多い」といった旨の指摘がされており、世間での注目度と実情に大きな差があると思われます。
*引用:経済産業省「2024年版ものづくり白書(全体版)」, p.204
製造事業者におけるDXは、依然として「個別工程のカイゼン」に関する取組が多く、「製造機能の全体最適※ 」を目指す取組は少ない。また、新たな製品・サービスの創出により新市場を獲得し、「事業機会の拡大」を目指すDXの取組は更に少ない。
※経営戦略の遂行に向け、製造部門だけでなく、設計、開発、調達、物流、営業等の部門とも連携し、例えば、原価管理、部品表、工程表の一元管理等を行うこと。
※経営戦略の遂行に向け、製造部門だけでなく、設計、開発、調達、物流、営業等の部門とも連携し、例えば、原価管理、部品表、工程表の一元管理等を行うこと。
備考:「わからない」及び「未回答」は集計から除いている。
資料: (国研)新エネルギー・産業技術総合開発機構「5G等の活用による製造業のダイナミック・ケイパビリティ強化に向けた研究開発事業/製造現場のダイナミック・ケイパビリティ強化施策と今後の普及に係る調査事業」にて実施したアンケートから経済産業省作成
資料: (国研)新エネルギー・産業技術総合開発機構「5G等の活用による製造業のダイナミック・ケイパビリティ強化に向けた研究開発事業/製造現場のダイナミック・ケイパビリティ強化施策と今後の普及に係る調査事業」にて実施したアンケートから経済産業省作成
今回私たちは、合同会社アルファコンパスの福本勲さんをお招きし、こうした製造業の現状に関する専門的な知見をお伺いしながら、今、そして将来、製造DXに向けて私たちNSWがどうあるべきかについてお話ししました。全3編におよぶ本シリーズのうち、Part1にあたる今回は「全体最適とは何か?」を中心にお話していきます。
対談者紹介
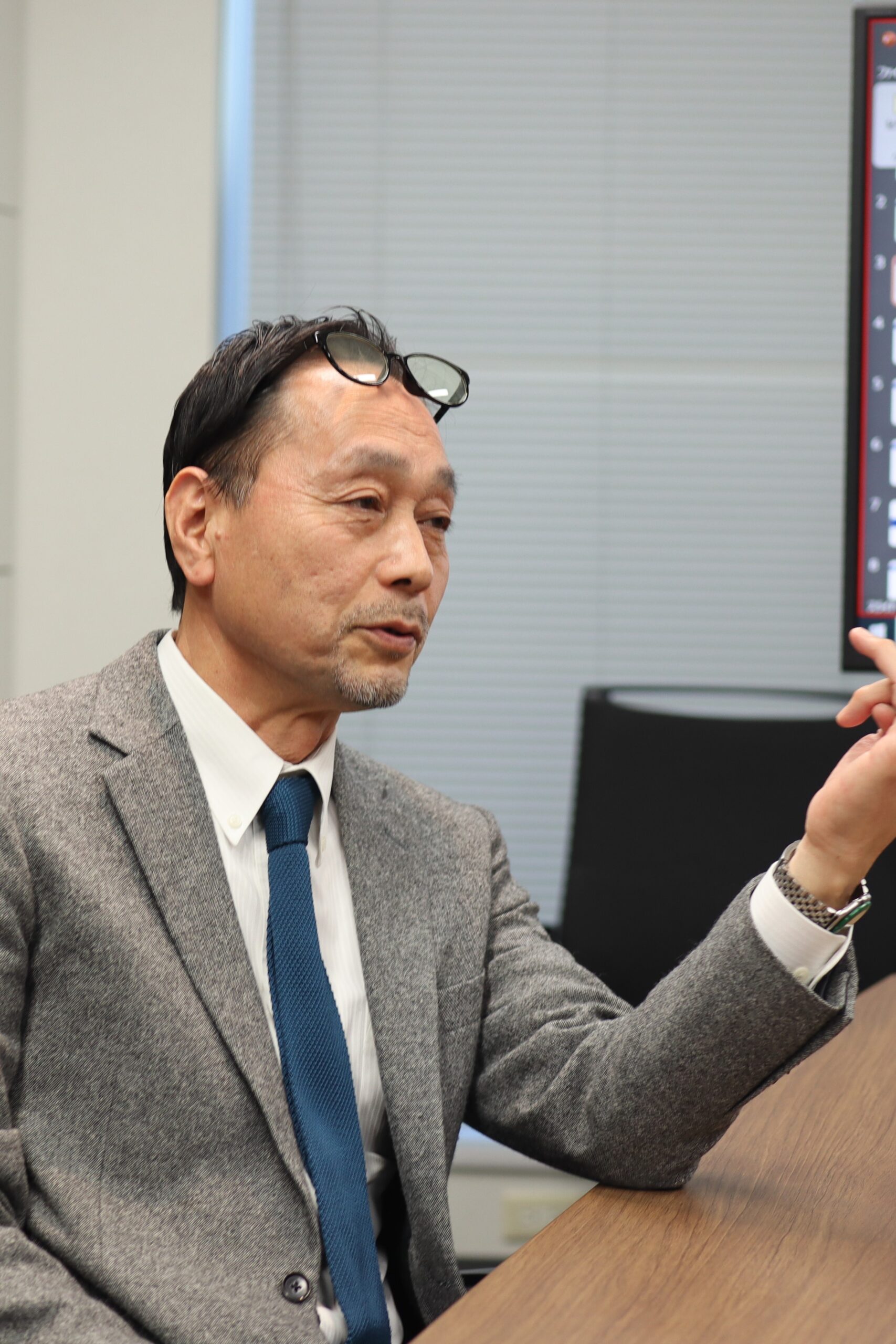
NSW株式会社
荒井 毅一
大手製造メーカーに勤務後、TPS(トヨタ生産方式)の社内展開、新規事業立上げなどを経てNSWに入社。国内・海外工場システム構築・展開など、特に製造分野に深い知見を持ち、顧客目線での、お客様のDX推進を支援しています。
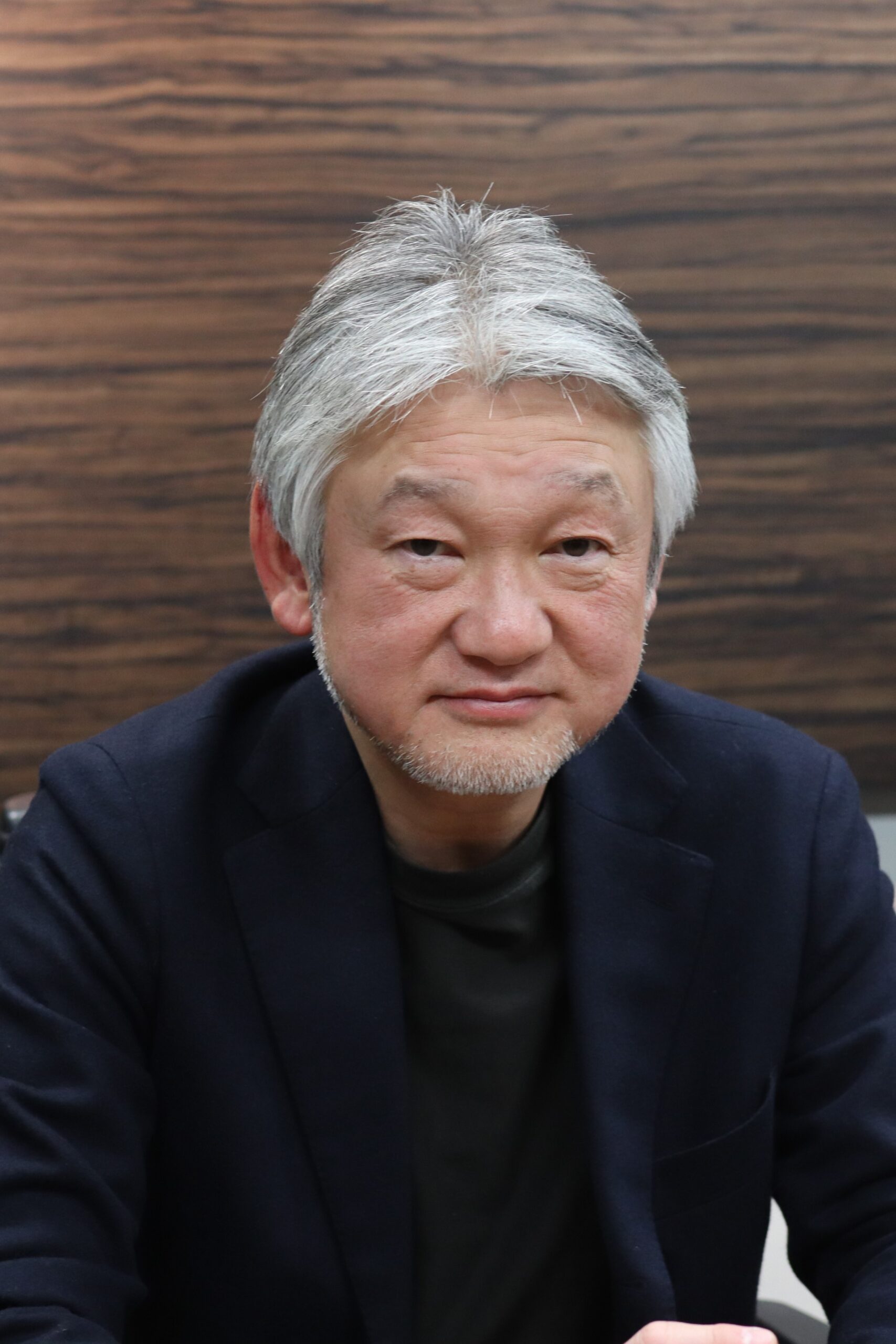
合同会社アルファコンパス
福本 勲
合同会社アルファコンパスの代表CEOを務め、製造業のデジタルトランスフォーメーションやマーケティング支援に注力しています。また、中小企業診断士としても活動し、講演や執筆を通じて製造業の変革を推進しています。
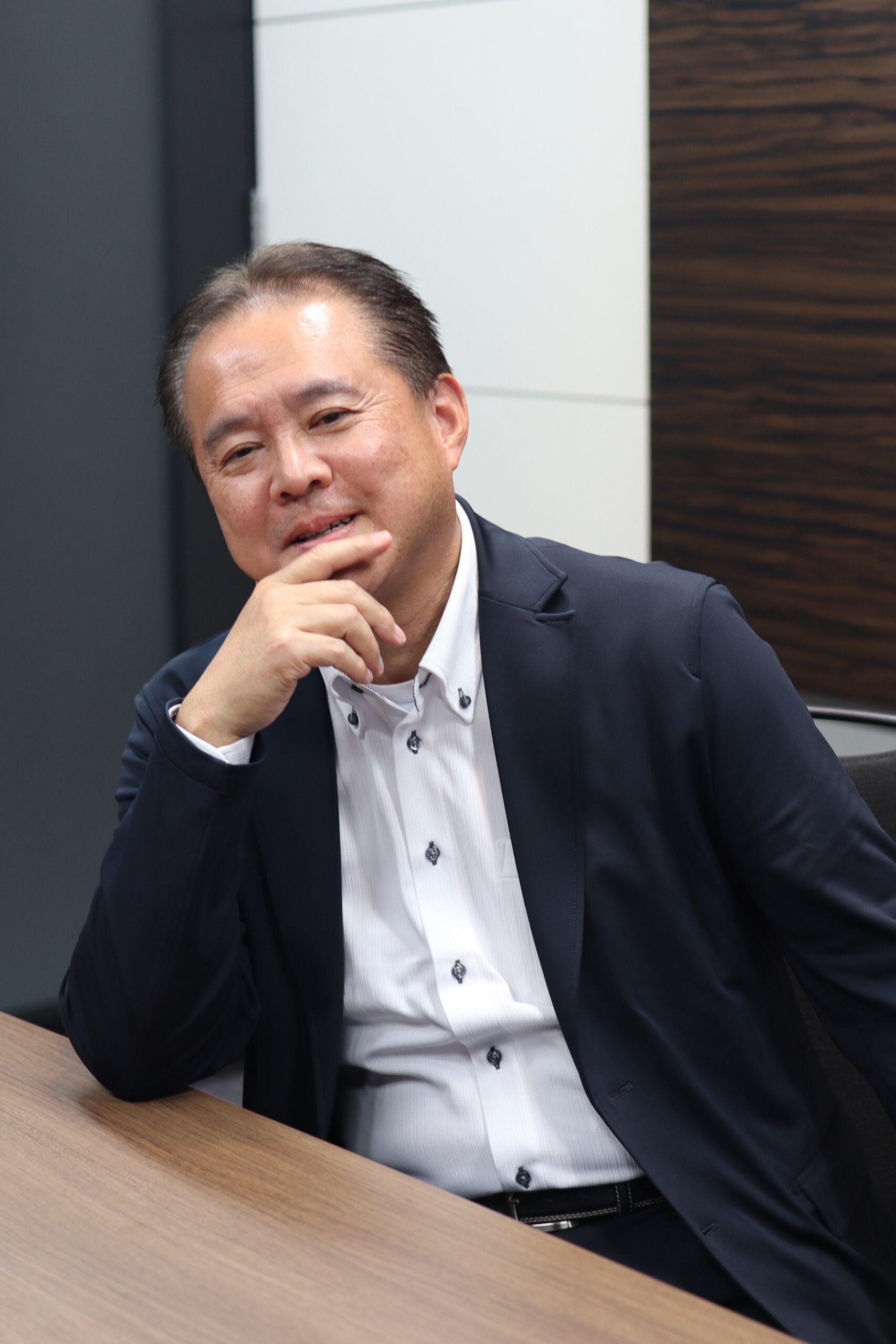
NSW株式会社
堀内 忠彦
大手精密機械メーカーに勤務後、コンサルタントを経てNSWに入社。お客様と共創、伴走するコンサル業務で製造業主体のDXを推進。技術士(経営工学部門)として、生産業務プロセス改善、SCM、現場改善指導等にも従事しています。
「ジャストインタイム = 全体最適」とは限らない?
*Ouranos Ecosystem(ウラノス・エコシステム)
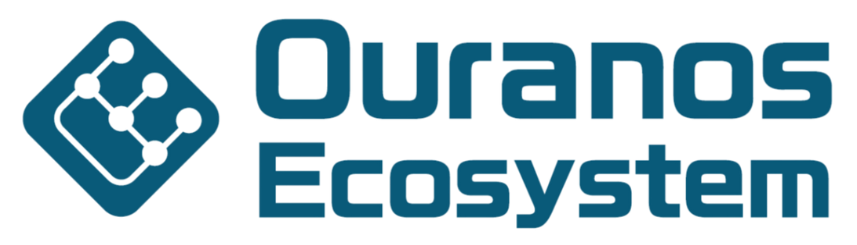
経済産業省が、関係省庁やIPA、NEDOと協力してエコシステムを構築し、経済の成長と、人手不足や災害の激甚化、脱炭素への対応といった社会課題の解決を両立させたSociety 5.0の実現を目指す取り組み。サイバー空間(仮想空間)とフィジカル空間(物理空間)を高度に融合させることで、経済発展と社会的課題の解決を両立する人間中心の社会を目指している。
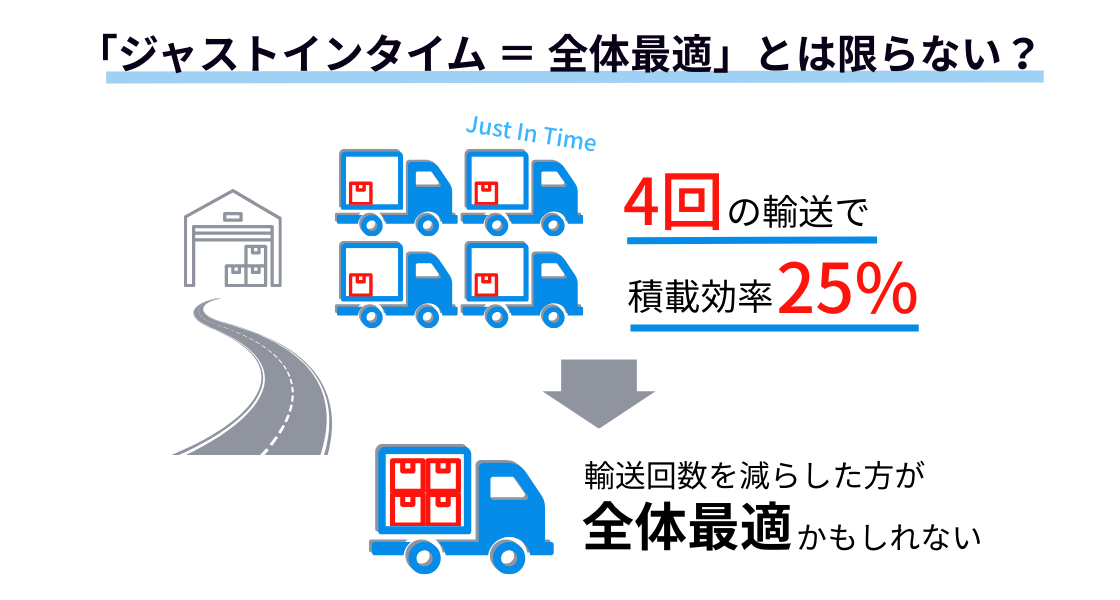
自分たちだけではなく、全体を変えていく
*物流の2024年問題
2024年4月1日から施行された働き方改革関連法により、トラックドライバーの時間外労働時間が年間960時間に制限されることに伴い、輸送能力の低下やドライバー不足の深刻化、運賃の値上げや物流コストの増加などを懸念する問題。この問題に対して、デジタル技術の活用や、荷主や消費者と協力して効率化する商慣行の見直しが必要とされている。
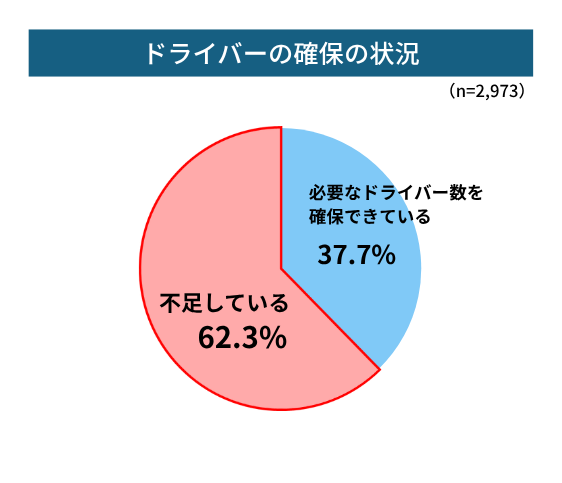
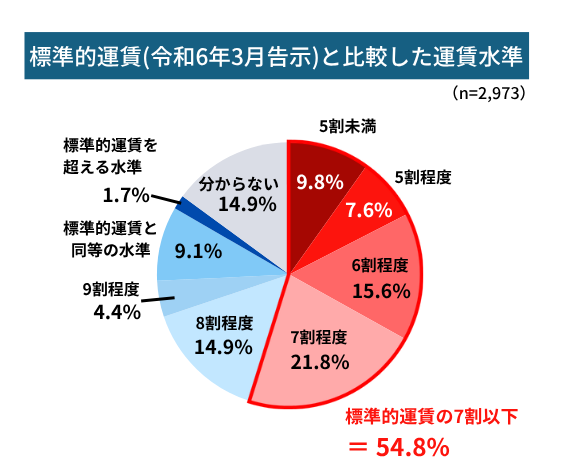
*ミカタプロジェクト
自動車産業に関わる中堅・中小企業が電動化やデジタル化(CASE:Connected, Autonomous, Shared, Electric)に対応できるよう電動車部品の製造や技術適応をサポートし、企業の事業転換や再構築を支援する取り組み。
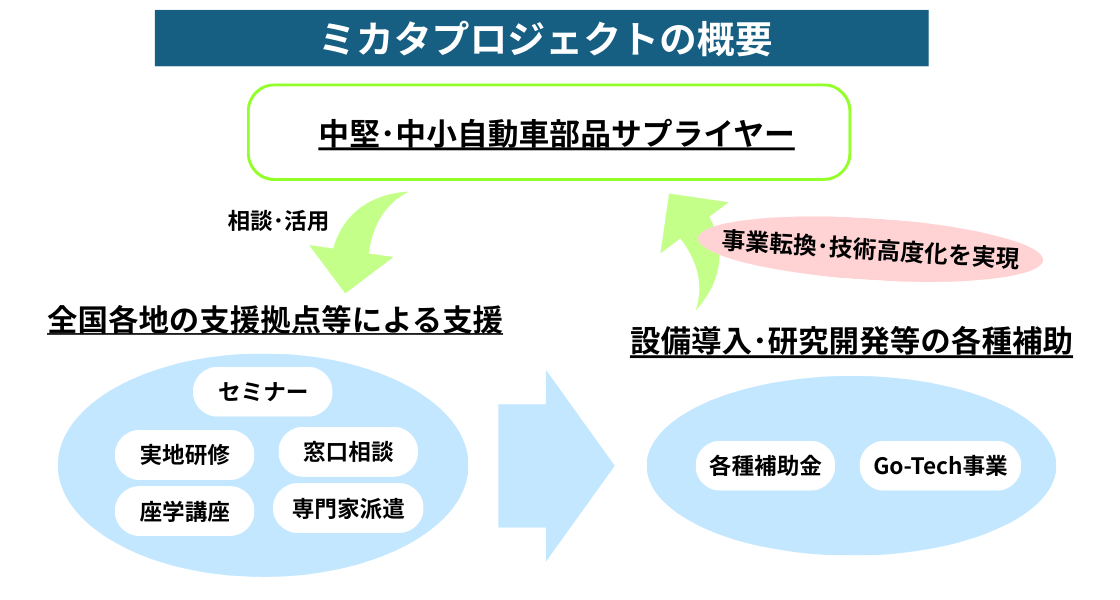
デジタル化した先で、データをどう扱うのか
*多角化度と収益性の関係
2024年版ものづくり白書では、事業や地域が多角化するほど収益性が下がる傾向にあり、さらにそれらが全体的に、欧米と比較すると日本企業が低いことが指摘されています。
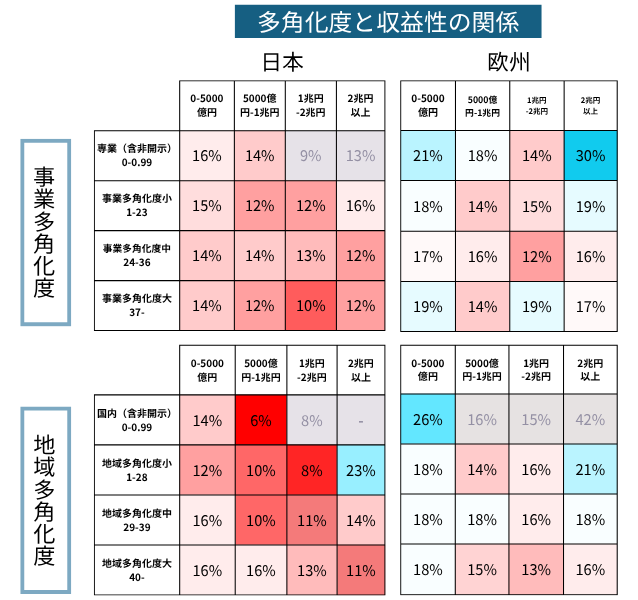
備考:Refinitivより取得した各企業のセグメントデータに基づき各国/地域内EBITDA実額上位500社(2023年時点直近会計年度末)の製造事業者を対象とし集計。着色の定義については、3か国(地域)の各セル内の収益性を横断的に比較し、収益性が低いセルは濃い赤、高いセルは濃い青といったグラデーションで示している。n数が5件未満の場合はグレーで示している。欧州対象国はEU先進16か国、EU非加盟先進4か国(スイス、ノルウェー、アイスランド、英国)で構成される。
資料:Refinitivより(株)NTTデータ作成(経済産業省「第2回グローバル競争力強化のためのCX研究会 資料3事務局提出資料」)
資料:Refinitivより(株)NTTデータ作成(経済産業省「第2回グローバル競争力強化のためのCX研究会 資料3事務局提出資料」)
*引用:経済産業省「2024年版ものづくり白書(全体版)」, p.193
現状では、多くの日本企業は、日本本社から海外現地法人を含む子会社へ人材を出向させることで間接的に本社の影響力を持たせる一方で、組織設計を始めとする様々な権限を子会社に委譲する「連邦経営」を行っていると言われている。その結果、それぞれの子会社に経理や人事等の機能が重複して所有され、固定費が膨張する一方で、各々が個別に制度・ルールを作り込むため、全社横断的なシステムやルールの整備・統一が進まず、急激なグローバル展開に伴う経営の複雑性の高まりともあいまって、非効率的な状況を生み出していると考えられる。
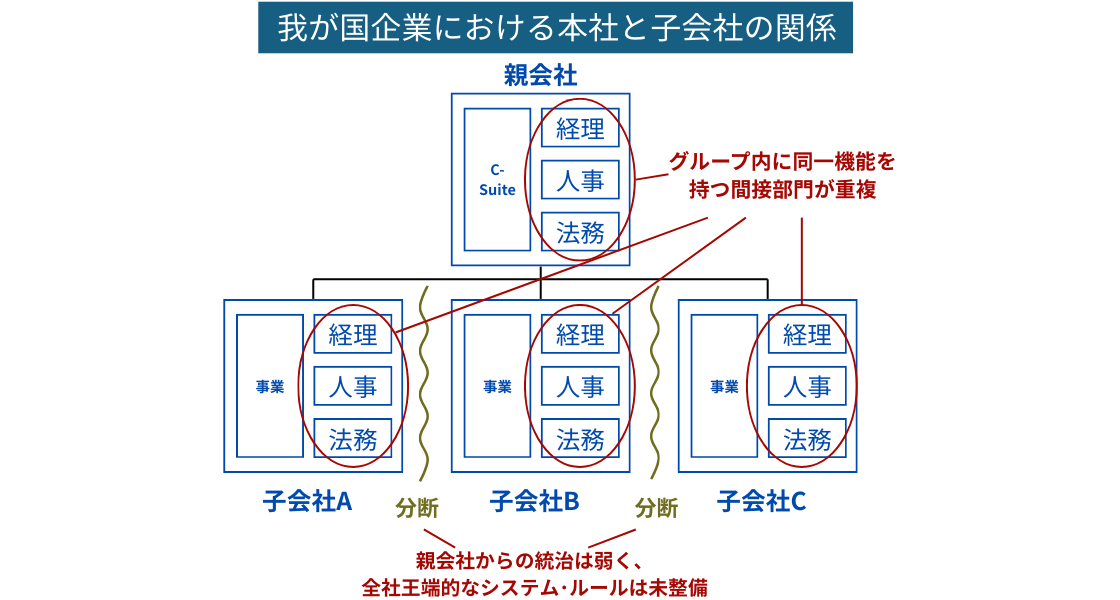
資料:(株)野村総合研究所「NRI Management Review 2011 Vol.26」や、デロイトトーマツコンサルティング(同)「グローバルビジネスにおける経営管理」などを参考に(株)NTTデータ作成(経済産業省「第4回グローバル競争力強化のためのCX研究会 資料3事務局提出資料」)
次のパートはこちらから
NSWが実現するDX
NSWは長年にわたる幅広い業種での豊富な実績と経験を生かし、お客様の潜在課題を多彩なデジタル技術で柔軟に解決することで、よりよい未来を築いていきたいと考えています。NSWの提供するスマートファクトリーソリューションもぜひご覧ください。