課題
- 生産状況や設備の稼働状況について、詳細状況を把握することで適切な改善活動につなげたい
- 製品不良や設備異常をリアルタイムに把握することで、即座に改善活動を開始したい
- 高品質な次世代自動車を安定生産するための生産技術を確立したい
解決策
- PLC、IoTセンサー、カメラなどの設備情報や、他システムからの情報をIoTプラットフォームに集約した
- 必要な情報を現場のニーズに合わせて組み合わせることで、改善活動に適したダッシュボードを作成した
- 内製化によるシステム改修期間の短縮を目指し、技術者育成のための教育を実施した
効果
- IoT化によるデータ収集・分析作業の自動化により改善活動の工数が50%以上削減
- システム開発技術者の育成が進み、現場のニーズに対して短期間でのシステム改修を実現できた
- リアルタイムに改善活動が開始できるようになったことで、生産時の各種ロスが削減できた
工場のIoT化で生産性向上を目指す日産自動車の挑戦 ー成功のカギは「標準化」にありー
「IoT化を進めたのに、思ったような活用ができていない…」こんな課題を抱えていませんか?
近年、多くの製造業が「工場のIoT化」を進めることで生産性向上や設備稼働率向上を目指しています。ですが、実際には「データは取れるようになったが、業務改善につながっていない」「導入後の運用が定着せず、システムが形骸化してしまう」という声も少なくありません。
日産自動車株式会社の生産ラインでも、同じ課題に直面していました。IoT技術を活用して設備や生産状況を可視化し、OEE(設備総合効率)改善を図ろうとしたものの、最初の試みでは期待通りの成果が出ませんでした。その大きな理由の一つが、現場のニーズをシステムに落とし込みきれなかった事です。システムの要件定義が現場の実態とずれたまま進行してしまい、導入したシステムが活かしきれない、現場スタッフが使いこなせないという問題が発生していました。そのような中、栃木工場にニッサンインテリジェントファクトリーに基づいた新しい生産ラインを立ち上げる事になり、この経験を糧に日産自動車は再挑戦を決意。新たなアプローチで「見える化」を進めることで、ついにOEEの改善につながる大きな成果を得ることができました。
「見える化」を機能させるためのポイントとは?
製造業におけるIoT導入は、技術的な側面だけでなく、「現場の業務プロセスとの適合性」や「データの活用設計」が鍵を握ります。
日産自動車が工場のIoT化を成功させた背景には、「データを可視化するだけでなく、現場で使われる仕組みを作る」 という考え方がありました。そこで、多様な設備に対応可能な接続モジュールと、標準化を実現するための仕組みが実装可能なPTCのIoTプラットフォーム「ThingWorx」を採用。
ライン稼働状況の見える化、生産状況の見える化、品質傾向の見える化 を3つの柱として導入。設備稼働率や良品率の向上、取得したデータを基に分析を実施し、データに基づいた品質とコストの管理を実現しました。
しかし、実現に至るまでには、単なるシステム導入だけでなく、どのデータをどう活用するのか、どのように運用定着させるのかといった具体的なプロセスが必要でした。その詳細なステップと、日産自動車がどのように「現場で活用できるIoTシステムの導入」を成功させたのか?その取り組みと手法を、ホワイトペーパーで詳しく解説しています。
工場のIoT化を推進し、OEE改善を目指す方は、ぜひご覧ください。
「工場の見える化」の取り組み背景や課題、解決方法をご紹介している、ホワイトペーパーです。
日産自動車が進めるOEE改善(ロス低減による生産能力向上)を目指したIoTシステム活用に関する全貌が明らかになっています!
■こんな方・企業におすすめ
・IoTの導入を進めてみたものの、うまく導入・活用できなかった担当者
・作業員の作業状況・進捗具合を把握する仕組みがなく課題を持っている管理者
・製造DXの知見者が在籍しているITベンダーを探している方
・段階を踏んだ製造DXの導入を検討していきたいが、うまく進められていない企画やDX推進者
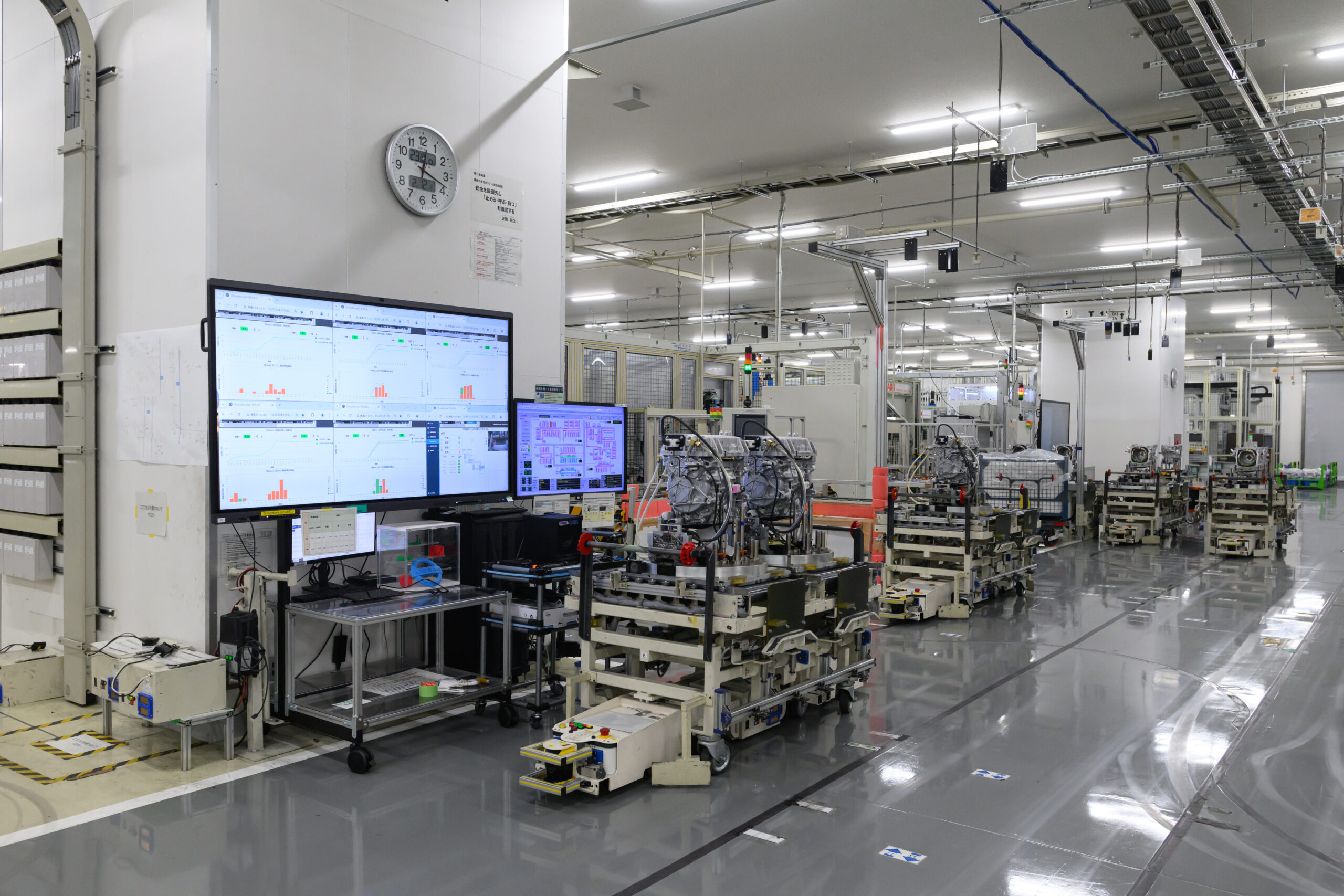
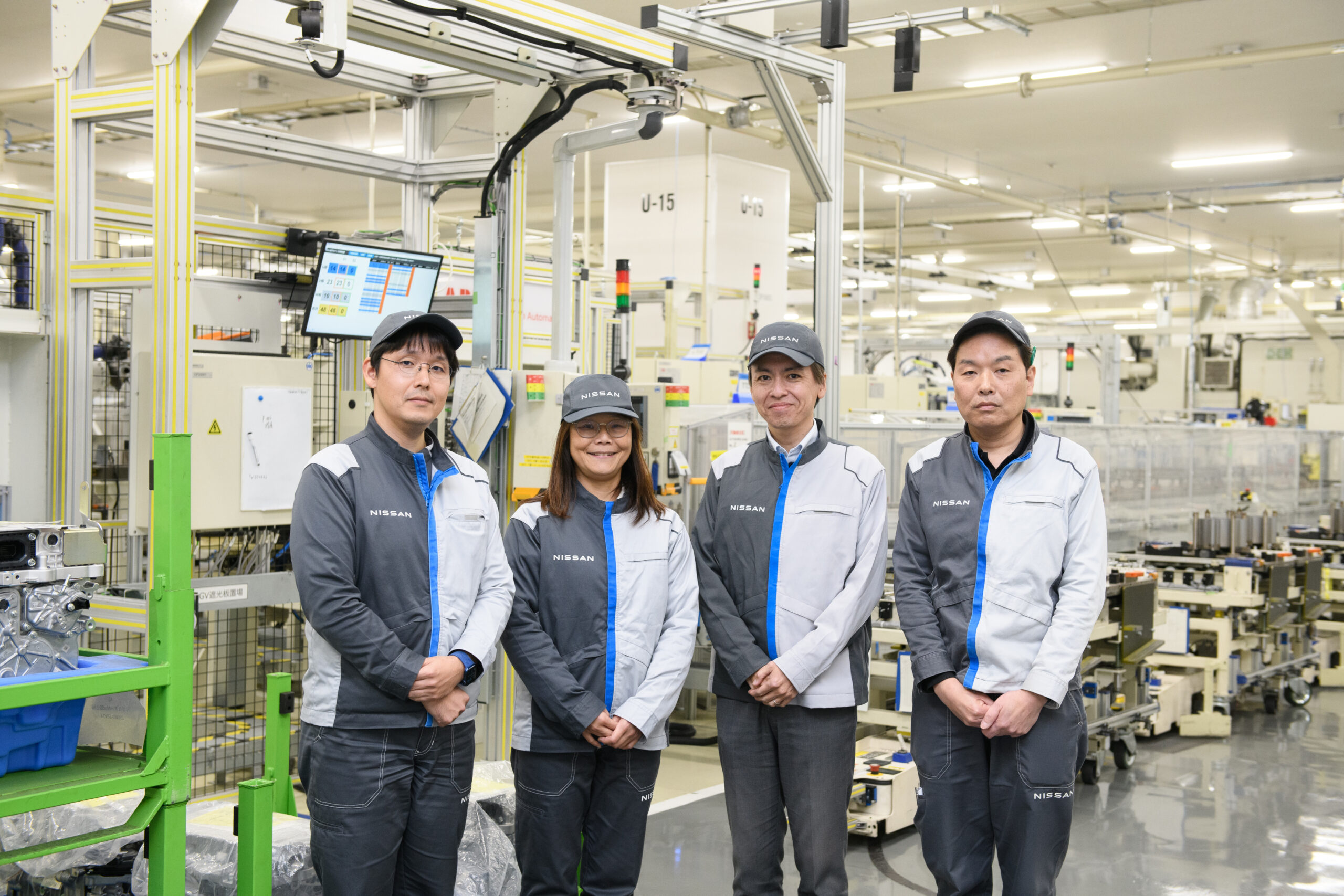
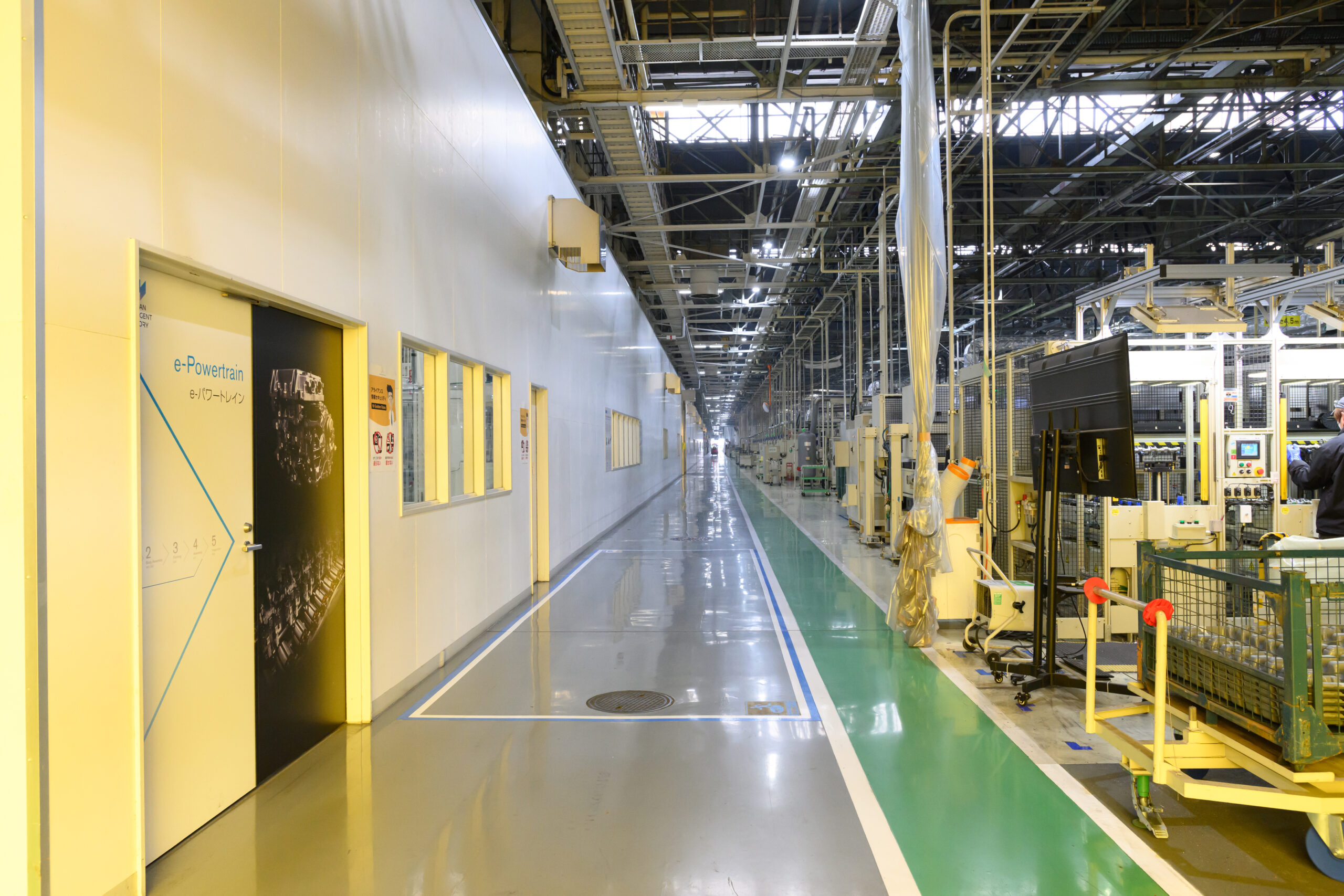
ThingWorxが実現する工場IoTシステム
設備データを活用し、工場の生産性向上を実現するためには、データの収集・統合・可視化・分析をスムーズに行える仕組みが不可欠です。日産自動車では、ThingWorxを活用することで、ラインを稼働するための大量の設備からリアルタイムデータを取得し、生産ライン全体の最適化を実現しました。
POINT01
多様なデータに対応した接続オプション
PLCやIoTセンサー、カメラなど
製造現場の多様な設備と接続します。
POINT02
標準化を意識した充実のテンプレート
見える化に必要なグラフや表など標準搭載。
開発経験がない現場スタッフでも作成・修正可能です。
POINT03
全てのデータを統合・管理
収集した様々なデータを集約し、生産状況、設備の稼働率、異常アラートをリアルタイムで監視。
OEE(総合設備効率)向上に貢献します。
POINT04
他システムとの連携による分析基盤
他システムとの連携が可能です。
企業が持つ様々なデータをThingWorx上に集め
データをもとにした生産効率改善に取り組む事が出来ます。
ホワイトペーパーでは、IoTシステムのシステム構成についてもご紹介しております。
「工場の見える化」の取り組み背景や課題、解決方法をご紹介している、ホワイトペーパーです。
日産自動車が進めるOEE改善(ロス低減による生産能力向上)を目指したIoTシステム活用に関する全貌が明らかになっています!
■こんな方・企業におすすめ
・IoTの導入を進めてみたものの、うまく導入・活用できなかった担当者
・作業員の作業状況・進捗具合を把握する仕組みがなく課題を持っている管理者
・製造DXの知見者が在籍しているITベンダーを探している方
・段階を踏んだ製造DXの導入を検討していきたいが、うまく進められていない企画やDX推進者